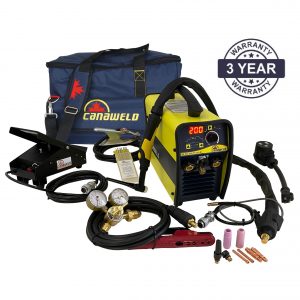
Aluminum is a versatile and popular metal construction material. Its lightweight, corrosion resistance and thermal conductivity make it popular in the aerospace, automotive, marine, and construction sectors. Tungsten Inert Gas (TIG) welding, known for its accuracy, cleanliness, and high-quality welds, is used by trained welders to maximize aluminum manufacturing. This article covers aluminum tig welder procedures, problems, and abilities needed to become successful.
Mastering Technique
Technical knowledge, expertise, and attention to detail are needed to master aluminum TIG welding. Here are some key aluminum TIG welding recommendations for beginners:
●Proper Prep
The aluminum surface must be thoroughly prepared before welding. This entails removing the oxide layer, oil, and grime using a stainless steel wire brush or chemical cleaner. Cross-contamination from steel brushes may be avoided by using a stainless steel brush.
●Electrode Choice and Grinding
Choosing the proper tungsten electrode is crucial. Pure tungsten or a tungsten alloy with thorium or cerium is best for welding aluminum. Grinding the electrode to a point ensures a steady arc and accurate heat input management.
●Heat Control
Aluminum warms and cools quickly due to its strong thermal conductivity. Welders must compromise heat input and travel speed. A smooth weld bead is achieved by controlling arc duration and travel speed to avoid burn-through.
●Filler Rod Control
Aluminum tig welder requires skillful filler rod handling. The filler rod should be dipped into the leading edge of the puddle to melt evenly and blend with the base material. Selecting the right filler rod size is essential for weld strength.
●Gas Shielding, Back Purging
An efficient gas barrier is essential in aluminum TIG welding. Continuous high-purity argon gas shields the weld pool from ambient contamination. Back purging using argon gas on the other side of the weld joint helps prevent oxidation and improve weld quality.
● Inspection and Cleaning After Welding
After welding, clean the surface to eliminate pollution. Use stainless steel brushes or chemical cleaning. The weld’s integrity and quality are also checked visually and non-destructively.
Conclusion
Becoming a skilled aluminum TIG welder takes time, effort, and knowledge of the material and procedure. Welders can make high-quality aluminum joints that match industry standards with the correct equipment, preparation, and expertise.